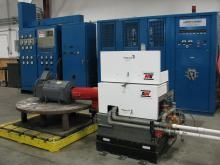
To ensure your motor operates properly upon installation, our team will use a dynamometer to provide simulated load testing. This allows testing of a motor's normal process and conditions to ensure that it will work at optimum capacity when you get it back. Testing with a dynamometer is the best way to qualify the quality of the repair and evaluate the performance of a motor. This also allows us to measure performance quality before and after service and verify motor performance records.
Core loss is the major cause of wasted electrical energy that can result from overheating during operation, motor burnout, or physical damage. Core loss testing ensures your motor is capable of operating at its rated efficiency. If your motor fails a core loss test it may end up costing more due to energy inefficiencies.
Electronic failures are responsible for 35% to 40% of all motor failures. It is important to run the proper tests to detect these failures before they happen. Through Surge Testing, DC Hi Potential tests and Polarization Index (PI) Testing, we can detect weak insulation issues that will cripple the life of your motor.
- Surge testing enables us to test the motor from phase-to-phase, phase-to-ground and turn-to-turn.
- DC Hi-Potential testing enables us to examine ground wall insulation that may be damaged due to breakdowns or high leakage currents. We also examine the slot liner, wedge conductors between the junction box and the coils.
- PI Testing enables us to examine the gradual deterioration of the insulation and the need for replacement.
Through a vibration analysis, Northwest Electric can pinpoint possible failures before they occur. It allows identification of problems due to imbalance, misalignment, resonance, bearings, motor components, etc. It also safeguards against equipment loss. Our team runs the analysis at full voltage for an extended period of time, and checks to ensure bearings are not defected or worn and mechanical fits are correctly in place.
Heat or high loads of stress may cause a shaft to bend. For the maximum efficiency of your equipment, our team can perform testing for Total Indicated Runout to ensure the shaft is straight and will not damage your motor due to running at a high vibration.
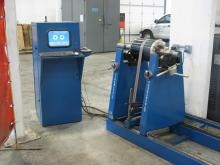
This test balances the vibration of a rotating piece of equipment. The balancer will analyze whether there is any imbalance in the shaft that can be addressed by the addition or subtraction of weight, ensuring that the shaft runs smoothly and efficiently without damaging your motor
We'll check the balances of ohms between the phases of your winding, making sure each one of them has the same level of ohms - which is critical for the efficient operation of a motor.
A broken rotor bar will negatively impact balance and the performance of the motor. This procedure ensures that the bars in your rotor are not broken or cracked.
Performing a bar-to-bar resistance check will indicate any shorted windings or defective solder joints at the risers of an armature. It ensures that the ohms of the windings are balanced and your insulation is intact. This is critical for the efficient operation of a DC motor.